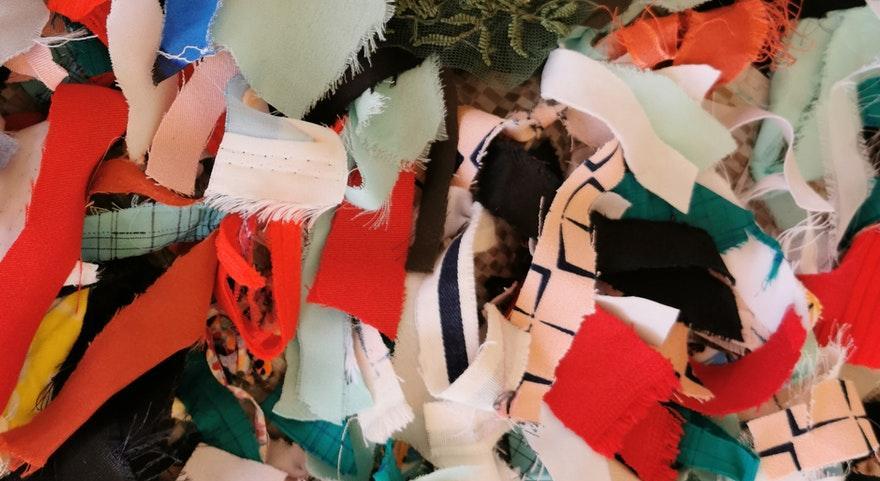
Textile Circularity Centre
Key York Contacts
Prof Neil Bruce, Centre for Novel Agricultural Products, University of York [co-lead]
Dr Alexandra Lanot, Centre for Novel Agricultural Products, University of York
Principal and Co-Investigators
Principal Investigator
TCC: Professor Sharon Baurley, Materials Science Research Centre, Royal College of Art
Material Circularity strand Dr Miriam Ribul, Materials Science Research Centre, Royal College of Art
Co-Investigators
Professor Neil Bruce, Centre for Novel Agricultural Products, University of York [co-lead]
Dr Alexandra Lanot, Centre for Novel Agricultural Products, University of York
Professor Prasad Potluri, Department of Materials, University of Manchester
Professor Paulo Bartolo, School of Engineering, University of Manchester
Dr Sameer Rahatekar, Enhanced Composites & Structures Centre, Cranfield University
Professor Phil Purnell, School of Civil Engineering, University of Leeds
Dr Vivek Koncherry, School of Natural Sciences, Department of Materials, University of Manchester
Dr Cian Vyas, School of Engineering, University of Manchester
Funder
UK Research and Innovation (UKRI) National Interdisciplinary Circular Economy Centres Research programme, and coordinated by the Circular Economy Hub.
External Partners
Professor Sharon Baurley (RCA)
Professor Phil Purnell (University of Leeds)
Cranfield University,
University of Cambridge,
University College London,
University of Manchester