Department of Computer Science
Dr John Oyekan (Computer Science), Ian Fairlamb (Chemistry), and Helen Sneddon (Chemistry)
Challenge: Chemistry, as a science, has undergone a transformation in recent decades, driven by the exponential growth of knowledge, increased demand for novel chemical compounds, and a greater focus on sustainability.
Furthermore, chemists are often exposed to hazardous chemicals during the investigation, exploring and synthesis of new materials. In order to advance the creation of new materials, we need to change the paradigm of synthesizing them. The ability of robots and automation to carry out tasks that are dangerous and dull provide a mechanism to exploit for the exploration of novel materials that have not been discovered yet.
Within this evolving landscape of discovering new materials, the quest for understanding reaction complexity and harnessing automated synthesis to create novel chemicals has taken centre stage. Chemical reactions have become increasingly complex, demanding a deeper understanding of diverse reactants, kinetics, and reaction pathways. Multistep reactions, intricate intermediates, and non-linear kinetics are just a few of the complexities that researchers face [1]. Understanding and optimizing these multifaceted processes is a bottleneck in fields ranging from pharmaceuticals to materials science.
However, the traditional laboratory setup, while invaluable, often faces limitations when dealing with the intricacies of modern chemistry. This is where the concept of flexible robotic labs comes into play, offering an innovative solution to the challenges of reaction complexity and automated synthesis. Automation has undoubtedly advanced our ability to tackle complex reactions. Automated systems offer precision, high throughput, and consistent execution. However, the conventional automation systems often lack the adaptability and decision-making capabilities required to manage the diverse spectrum of complex chemical processes. Reacting to changing conditions and unexpected variations is a challenge [2].
Proposal: Flexible robotic labs, a novel paradigm in chemical research, represent a promising solution. These labs integrate advanced robotics, artificial intelligence, and adaptive sensors within a modular and adaptable workspace. Researchers can reconfigure the lab's layout and instrumentation to suit the specific requirements of their projects, thus providing an environment that is both versatile and customizable [3].
This 3 year PhD programme will investigate the following hypotheses: Flexible customization and scalability of Automation Systems Enable Broad Applicability Across Chemical Domains leading to more sustainable chemical processes.
Objectives: The following objectives will be investigated:
Objective 1. Reaction Monitoring and Optimization: One of the primary challenges in automated synthesis is the real-time monitoring and optimization of chemical reactions. Automation systems must be capable of accurately assessing reaction progress, adjusting reaction parameters as needed, and ensuring the desired outcome. Developing robust sensors and control algorithms for various reaction types is a research area that would be investigated through the use of off the shelf components as well as 3D printed parts. This approach would support us in developing automation hardware that is versatile and adaptable to handle different reactors, reagents, and conditions for various reactions
Objective 2. Handling Complexity: Many chemical reactions are highly complex, involving multiple steps, reagents, and conditions. Automating such intricate processes demands advanced programming and robotics capabilities to handle the diverse requirements of different reactions. Research will be carried out to design versatile automation systems that can adapt to various levels of reaction complexity.
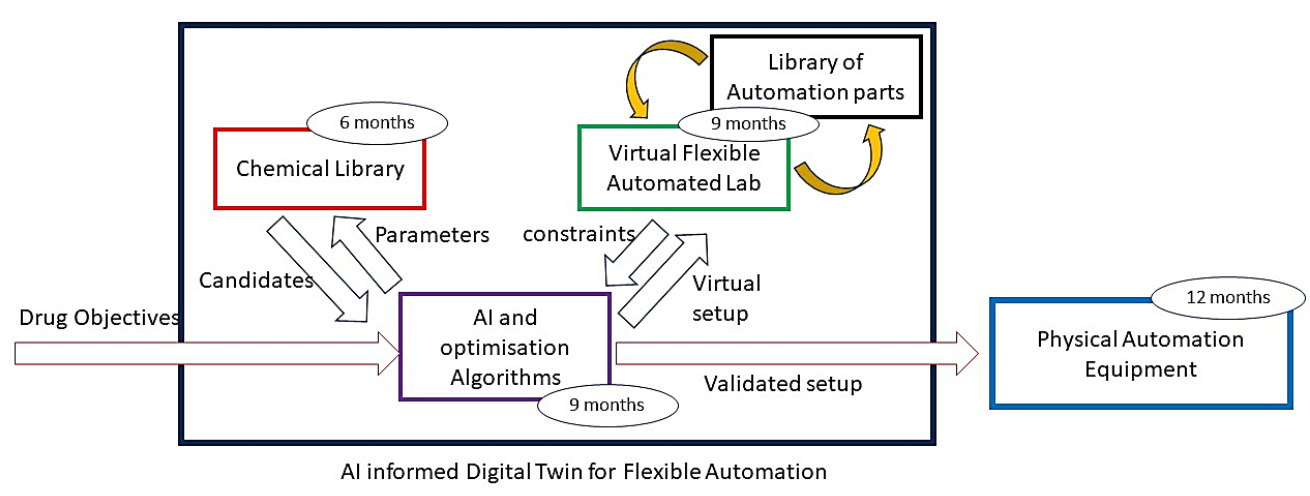
Figure 1. The breakdown of tasks and duration of each
Objective 3. Integration with AI and Machine Learning: The integration of artificial intelligence (AI) and machine learning presents a significant opportunity to improve the efficiency of automated synthesis. However, challenges include developing AI algorithms that can accurately predict reaction outcomes, optimize conditions, and adapt to unforeseen variations. This stage of the PhD research will focus on creating AI models capable of handling the complexity of chemical systems. The first step would making use of data from various chemical reaction databases. Also, an investigation will be carried out into the use of Generative AI and Large Language Models to support the discovery of novel chemicals.
Objective 4. Synthesizing a flexible automated framework: Using the results obtained from objective 1 to 3 above, a framework would be developed. This framework would support the development of various flexible automated platforms for other biotechnology and chemistry domains looking to apply both AI and automation in the control of various chemical/biological reactors.
PhD programme tasks (See Figure 1): The objectives mentioned above will be achieved through the following tasks:
Literature review and down selection of drug candidates (6 months): This task would involve an extensive literature review that would look into various chemical and medicinal journals to find a range of potential chemical candidates that are disparate enough but also within the constraints of the physical lab equipment. The idea is that the down selected candidates would be capable of testing the flexibility of the automated framework being developed.
Development of a Virtual Flexible Automation Lab (9 months): This will involve searching for potential software that can be applied in developing digital copies of physical chemistry equipment. The chosen tool must be able to be flexibly reconfigured with APIs to chosen various components from a library and tune them. Tuning the library of components would ensure that any physical constraints are respected.
Development of AI and Optimisation Algorithms (9 months): This task will involve the development of and application of population based many-objectives algorithms. The challenge here would be integrating the constraints obtained from virtual flexible automation lab into the population based algorithms. Another challenge is converting the multiple objectives in the chemical space into a form that the optimisation algorithms would work upon. This work will build upon many-objective algorithm development that is being carried out in Computer Science.
Development and Integration with Physical Equipment (12 months): This task would involve understanding the physical equipment in the laboratory and investigating ways by which they can be adapted to work with the developed flexible automation framework. This work would also involve integrating PC controlled hardware (e.g labview cards) towards controlling various hardware in the lab.
Summary: As technology continues to advance, flexible automation is poised to become a paradigm shifting tool in supporting the investigation of complex reactions and contributing to the advancement of chemical science. The result of this PhD would be a framework as well as associated algorithms that would support the research community in exploring new materials. This would empower researchers to tackle intricate chemical challenges, drive advancements in various industries, and contribute to the sustainable and efficient practice of chemistry.
References:
[1] Hu, Y.J., Chen, J., Wang, Y.Q., Zhu, N., Fang, Z., Xu, J.H. and Guo, K., 2022. Biocatalysts used for multi-step reactions in continuous flow. Chemical Engineering Journal, 437, p.135400.
[2] Melin, J. and Quake, S.R., 2007. Microfluidic large-scale integration: the evolution of design rules for biological automation. Annu. Rev. Biophys. Biomol. Struct., 36, pp.213-231.
[3] Roughley, S.D. and Jordan, A.M., 2011. The medicinal chemist’s toolbox: an analysis of reactions used in the pursuit of drug candidates. Journal of medicinal chemistry, 54(10), pp.3451-3479.
Apply for this Project