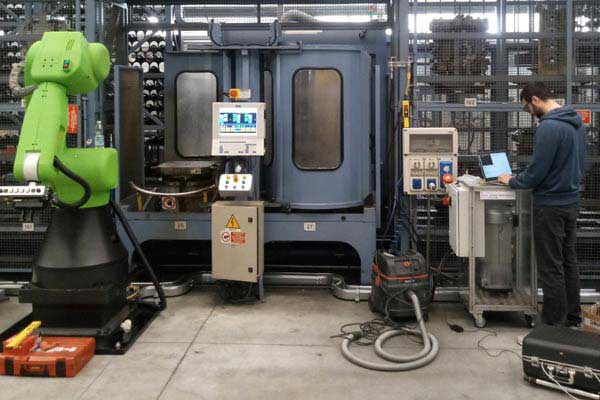
Safety of REconfigurable COLLaborative robots for flexible manufacturing systems (RECOLL)
Improving safety and productivity in manufacturing by studying human-robot interaction when using collaborative robots.
This project studied the safety-related human-robot behaviours when the operations in a prototype machining production setup need frequent reallocation of human/robot tasks, uneven distribution of human location, and subtask-dependent potential physical interaction with machines.
Contact us
Assuring Autonomy International Programme
assuring-autonomy@york.ac.uk
+44 (0)1904 325345
Institute for Safe Autonomy, University of York, Deramore Lane, York YO10 5GH
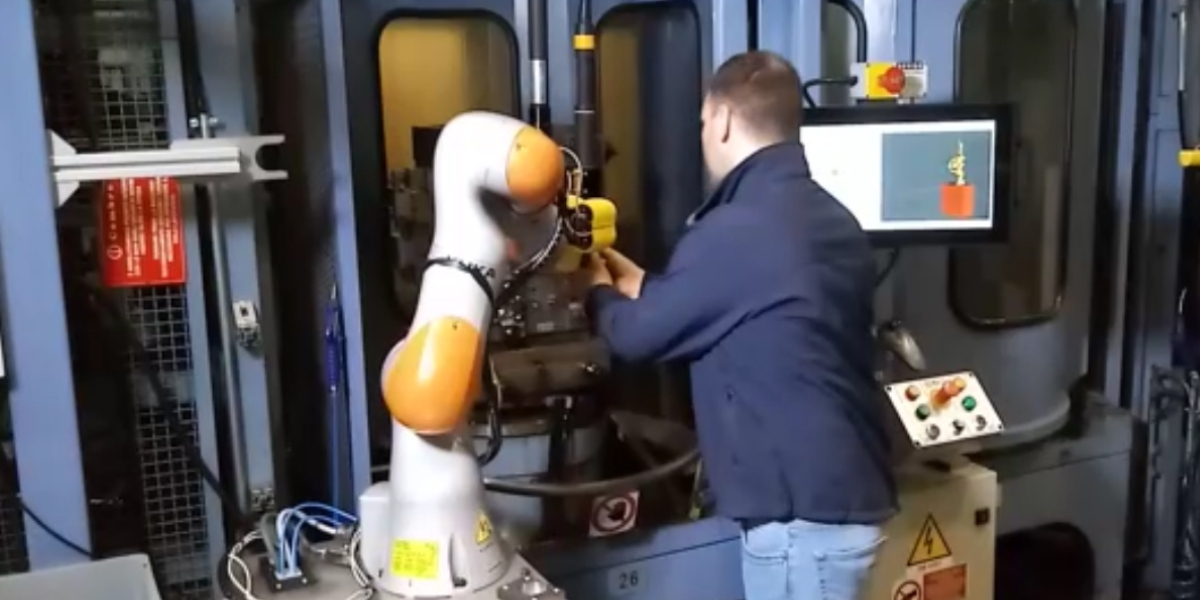
Project report
A full project reporting the team's research on improving safety and productivity in manufacturing when using collaborative robots.
The challenge
Collaborative robotics can transform the role of operators of flexible machining systems, allowing them to take on more value-added tasks, leaving robots to do repetitive or assistive tasks within the same shared workspace. At the same time, operator safety during hybrid tasks dealing with dynamic allocation or layout changes has to be assured.
The research
This project studied the safety-related human-robot behaviours (e.g. movements, layout occupation, voluntary/accidental contacts, near misses, etc) when the operations in a prototype machining production setup need frequent reallocation of human/robot tasks, uneven distribution of human location, and subtask-dependent potential physical interaction with machines.
The preparation of the work cell allowed the team to consider all intended uses by the operators. This was coded as the default expected pattern to be recorded with external sensors. A model of the collaborative task, including steps, notable positions, expected occupancy of the layout, etc. was formalised for tracing the online behaviour of both the robot and the human operator(s). From such records, the team was able to identify the principal components of the regular figures of human-robot collaboration (rate of task sharing, occupancy, distances, contacts, etc.) and the potential deviations.
Using sensors combined with a software tool that tracks human movements ensured the work cell was capable of recognising situations that can lead to undesired risks. The team collected a considerable amount of data related to a group of operators and the analysis helped to determine the probability of a hazard and its correlation with an incorrect task execution by the operator and/or an incorrect task planning by the system itself.
The results
The team developed a method for the quantitative evaluation of the safety risk assessment procedures, in line with current standards. In particular, possible differences within the number of hazardous situations occurring during human-robot cooperative tasks were addressed. This methodology can be applied to a wide range of human-robot collaboration scenarios. It allows us to understand if the preliminary risk assessment correctly includes all the possible hazardous situations and if its conservative approach will affect the cell’s productivity.
Contact us
Assuring Autonomy International Programme
assuring-autonomy@york.ac.uk
+44 (0)1904 325345
Institute for Safe Autonomy, University of York, Deramore Lane, York YO10 5GH