Slippery Sugar-Coated Surfaces Repair Themselves
Using nature for inspiration, a team of scientists in the UK and China has developed low-friction surfaces that have been designed in such a way they can repair themselves if damaged. These smart materials might one day be used in medical implants, like hip replacements.
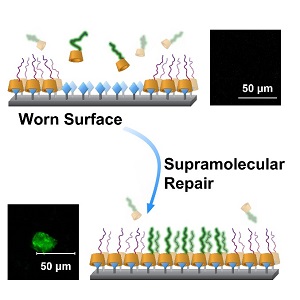
The new sugar-coated surfaces mimic the way cartilage works to lubricate our joints. Cartilage uses water to make a slick surface that minimises wear and tear. In the same way, the new coatings coax a layer of water to the surface, making it slippery and protecting the surfaces as they are knocked or rubbed. If cartilage becomes damaged, it can usually be repaired by the body, but artificial surfaces are not normally repaired so easily. This is the problem the new materials aim to solve.
The artificial polymer coating has two major parts. Firstly, it has a long molecular chain with positive and negative charges to hold onto a water layer – using an effect similar to static electricity. A sugar ring is then attached to one end of the chain. This ring anchors itself to a surface by docking with specific molecules, called adamantanes in a ‘molecular recognition’ process. Treating titanium metal with these adamantane structures, allowed the polymer coating to adhere to the surface. The reversible interactions that form are key to the repair.
“This is dynamic yet selective chemistry, which looks like it could be an effective way to limit the negative effects of mechanical wear on joints and other surfaces,” said Dr Alyssa-Jennifer Avestro, a Dorothy Hodgkin Research Fellow at the University of York and an author of the study. “If our protective coating layer is worn off, it is restored again without needing our intervention, as the interactions that hold the polymer to the titanium surface can re-establish themselves.”
For now, an efficient repair process requires more polymer coating to be dissolved in the water surrounding the surface. But the researchers believe it won’t be long until the coatings are improved to avoid the need for this extra material to be present. Ultimately, it is hoped these types of coatings will extend the lifetimes of joint replacements. The researchers also hope their design will inspire other chemists and engineers to develop new and improved low-friction surfaces based on molecular recognition strategies.
Creating artificial materials capable that are compatible with artificial joints and capable of self-repair has required the expertise of an international team of mechanical engineers and chemists. Yulong Sun, a researcher working with senior author Dr Paul McGonigal in Durham University, spent time investigating the low-friction surfaces with Yixin Wang and Hongyu Zhang in Tsinghua University’s Department of Mechanical Engineering in China. He bridged the gap between the chemical expertise needed to make the coatings and the engineering techniques used to measure their function.
Dr Paul McGonigal added “The components of our coatings are biocompatible, which makes them exciting prospects for use in medicine. However, we could also imagine developing a range of these materials that work in very different environments. Avoiding and repairing the damage caused by friction is equally important to ensure that cars and other machinery last for a long time.”
The research paper is published in Chem.
Dr Alyssa-Jennifer Avestro is partly of the recently-established ‘Molecular Materials’ research grouping in the Department of Chemistry at York. This group aims to explore a molecular approach to materials science, in which molecular recognition plays a key role in fabricating materials for a wide-range of high-tech applications.